
"You Dont Have to be Smart ...you just have to be smart enough to learn from others."
August 1, 2012Comments
I love that quote, and wish I had come up with it. But alas, it comes from Jim Zawacki, owner of metalforming company GR Spring & Stamping Co., Grand Rapids, MI. He slipped those words of wisdom into the conversation during an interview with contributing editor Louis Kren for an article that appeared in the July 2012 issue of MetalForming.
Zawacki’s point, as presented by Kren, emphasized a leadership strategy rooted in continuous learning. If your company’s leadership isn’t interested in developing a learning culture—not just in the shop, but throughout the front office—then turn the page. If it is, keep reading.
“It’s time for people development,” writes blogger Jason Piatt, a consultant to manufacturers on lean, Six Sigma and strategy formation. “During the downturn, training budgets were slashed…looking ahead to the next downturn, managers should consider what capabilities their staff needs to develop to better handle economic fluctuations. Some considerations might be change management, technical training and development of leadership skills.”
Creating a learning culture does more than just deepen the knowledge base at your company. It creates what author and consultant Brad Hams calls “Ownership Thinking.” I met Hams at the MFG (Manufacturing for Growth) meeting held last March in Orlando, FL, and strongly recommend his book: Ownership Thinking. Hams describes three components of ownership thinking: the right incentives, the right education and the right measures (to go along with the right people). The end to these means, says Hams: “The creation of an organization whose employees think and act like owners toward creating wealth.”
This is precisely the goal of the Precision Metalforming Association’s new Management Development Academy (MDA), introduced in an article beginning on page 38 of this issue. Here’s what PMA chairman P.J. Thompson, who helped launch the MDA, says:
“The learning does not stop when the program ends—continuous improvement applies here, just as it does in the shop.”
Where should metalformers focus their education efforts? For starters, pay close attention to servo-press technology. Get started by reading the article beginning on page 24 of this issue, titled, Take What You Know About Stamping Presses and Throw it Out the Window. Early adopters of servo presses will soon—if they haven’t already—leapfrog their competitors in the race to gain new customers.
Want to learn how metalformers are growing their businesses by investing in servo-press technology? Invest a little of your time to attend (free of charge) a three-part webinar series addressing servo-press technology from several angles, and then visit PMA headquarters for a half-day seminar. The webinar series launches Thursday, August 23, with an overview of servo-press technology and its applications. On Thursday, August 30, the second webinar in the series will provide an in-depth look at specific applications for servo presses—deep drawing and in-die secondary operations. Webinar three (Thursday, September 6) will address marrying a servo press to a metalforming system—considerations for controls and feeds.
Lastly, we invite metalformers to PMA headquarters in Cleveland, OH, on September 19, for a half-day event featuring case-study presentations and breakout sessions.
Visit www.metalformingmagazine.com/servo to learn more and register to attend.Technologies: Management, Training
Comments
Must be logged in to post a comment. Sign in or Create an Account
There are no comments posted.Laurie Harbour, President, Harbour Results, Inc., E707
Wednesday, January 24, 2024
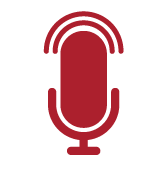
MetalForming LIVE 2024: Recruit, Retain, Train Reca...
Monday, January 22, 2024
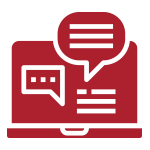