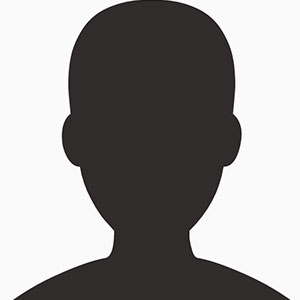
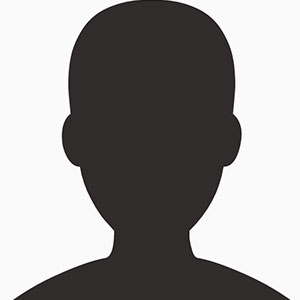
Extending the Life of Welding Guns and Consumables
March 29, 2024Comments
Attention to maintenance details along with proper care of cables, connections and more go a long way in extending consumables life and maintaining high-quality gas-metal-arc welding (GMAW).
Care for the Cable
Be sure to keep up with maintenance. At the beginning of every shift, welders should inspect the gun handle to make sure it is not broken. A broken handle can lead to safety and performance issues. Ensure that all screws are tight; you don’t want them falling out during or after a welding job. Next check all connections—contact tips and diffusers. Throughout the life of the contact tip it will loosen, so it is important to tighten regularly.
The strain relief on the welding-torch cord is there for a reason. From time to time welders cut it off. Why? Perhaps for ergonomic reasons—to make the gun easier to hold. However, removing the strain relief comes with its own set of problems. When it’s removed, the plastic gun handle can cut through the cable and damage it, exposing bare wires. This is a huge no-no, especially as it’s located so closely to the welder’s hand.
However, it is more likely that removing the strain relief will cause a kink in the gas-flow tube located inside of the cable. The tube could become kinked and cut off the flow of the shielding gas, which causes porosity in the weld.
A welder may not recognize kinking as the cause, and waste time and effort searching for other causes of porosity. Even with the strain relief attached, be mindful of possible kinks in the cable that can impede gas flow and, again, introduce porosity. While gas problems most often cause porosity, a welder may choose to chase down other possibilities while a quick check of the cable can head off the problem right away.
Damaged power cables can lead to a gas leak or an open electrical circuit. This happens when the cable receives cuts, nicks or tears in the jacketing. Electrical tape is not a quick fix and OSHA will agree. Thick patches such as 600-V heat-shrink wrap will work, but will prevent bending of the repaired area of the cable, which can be a nuisance. We recommend a complete repair. Some welding manufacturers offer a fully repairable welding-gun setup where users can remove a bad cable section and reterminate the cable, but this will result in a shorter cable length.