Sales Process Delivers Results
![]() |
Stamping throughput—total revenue minus outsourcing and material costs, divided by the number of full-time employees—continues trending upward. Bars show the average value-added revenue per full-time employee in thousands of dollars. |
For example, an analysis of the company’s current request for quote (RFQ) hit-rate data across customers, jobs, type of work, etc., could provide insights that help drive strategy. This analysis, which reveals the number of quotes per customer, number of quotes won per customer, total value of the business won and total value of the quotes requested, enables a shop to determine its low- and high-volume customers and whether its business is appropriately diversified among customers and/or industries. Along with the company’s overall business strategy, this data provide the information needed for identifying sales opportunities and challenges, serving as the foundation for building an effective sales process.
Creating Operational Excellence
Advancements in pressroom automation equipment and software, when integrated with game-changers such as big data, the Internet of Things, virtual reality and artificial intelligence, point to a new era for metal formers and fabricators. Companies must find ways to continuously evaluate technology and opportunities to eliminate waste in all processes, both physical and transactional, and adopt automation that fits their business strategies.
One such practice, capacity planning, measures the maximum amount of work that a shop can complete during a given time period. Though this can be challenging, capacity planning provides a number of benefits:
- Better on-time performance (fewer missed delivery dates), resulting from understanding the time needed for jobs;
- Mitigation of margin erosion through better management of materials and resources, including predicting and filling the gaps, and accounting for quality issues and changeover times;
- Recognition of new-work opportunities by predicting gaps in equipment/tonnage and space;
- Improved profitability resulting from effective planning capacity throughout the organization; and
- Effective budgeting for new equipment and additional resources, made possible by knowing the shop’s production capabilities.
Finally, shops should consider implementing task-based manufacturing to improve efficiency while maintaining or improving quality. By aligning roles and responsibilities by task, shops can better leverage the skills set of individual employees and capitalize on their ability to complete a task in the most effective manner. This translates to improved throughput and increased capacity without significant capital expenditures.
Task-based methodology, when not limited to the shop floor, can benefit the full enterprise. While challenging, companies that successfully accomplish this will see significant improvements as they reduce lead times and labor hours.
Moving forward, leadership must be informed and aware of several evolving areas, including the political environment, economic landscape, automotive industry slowdown, Industry 4.0, new technology such as 3D printing, the use of big data, and future mergers and acquisitions. MF
See also: Harbour Results Inc.
Technologies: Management
Comments
Must be logged in to post a comment. Sign in or Create an Account
There are no comments posted.Laurie Harbour, President, Harbour Results, Inc., E707
Wednesday, January 24, 2024
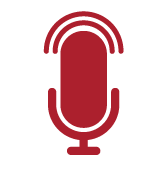
MetalForming LIVE 2024: Recruit, Retain, Train Reca...
Monday, January 22, 2024
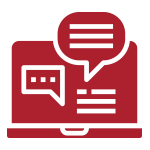