Metal AM’s Advantages Over Metal Injection Molding
December 5, 2022Comments
The decision to use metal 3D printing or metal injection molding (MIM) largely rests on part volumes required. However, the ability to employ metal additive manufacturing (AM) with investment in a new mold puts a check mark in the metal-AM box, according to information provided by 3DEO.
Prior to the advent of 3D printing with metal, manufacturers searching for a cost-effective way to make small and complex metal parts for production basically had two options: MIM or investment casting. Metal 3D printing adds another option to the engineer’s toolkit, with new low-cost, high-volume metal-AM technologies beginning to change conventional manufacturing wisdom.
Why MIM?
Today’s best MIM operations have proven that MIM is capable of reliable high-volume production that yields strong material properties. Manufacturers employ MIM to create components in numerous markets including medical, firearms, general industrial and others. When a part design is not likely to change for the next 5 to 10 yr. due to a long design-in cycle, and part volumes will be in the hundreds of thousands to millions, investing in MIM tooling can make a lot of sense. Manufacturing engineers less painfully can write $50,000 or $100,000 checks when they know that cost of the mold will be amortized quickly over millions of parts.
Until now, very high costs per part held metal AM back. For example, powder-bed fusion machines can cost upward of $1 million, with material that may exceed $150/lb. These costs, in addition to other labor and infrastructure costs, translate directly to a prohibitively high part cost.
MIM Limits Prove Frustrating
Many engineers find frustration with MIM in that, aside from the high-cost tooling, the process is limited to a single component per mold. The desire to produce 10 different parts requires investment in 10 different molds. A small feature change to a part means modifying the existing mold, fixing the parts during post-processing, or investing in a completely new mold. Metal AM, on the other hand, holds the promise of freedom from the mold. Changing the design of the part is as easy as updating a computer file.
Also, MIM brings more constraints regarding part geometry than metal 3D printing, due to the need for a mold, the need to force binder and powder under high pressures, and then the need to open the mold and extract green parts. Conversely, creating parts via 3D printing on a layer-by-layer basis enables new design freedom. Unlike MIM, additional complexity in metal AM does not also result in additional mold and production costs.
Assist From Bind-and-Sinter Technologies
Advances in bind-and-sinter technologies have provided a boost in metal AM’s ability to compete with MIM on a cost-per-part basis. These technologies employ a binder in a layer-by-layer process to create a “green part” that then is placed in a sintering furnace to reach full density. Reaching temperatures exceeding 2400 F is expensive no matter the process used, but having to reach it in every layer increases the cost of powder-bed fusion technologies.
Printing green parts in high volumes on lower-cost machines and then bulk-sintering all the parts at once can reduce costs significantly. Separating the various bind and sinter technologies: how the green part is created. Binder jetting employs an inkjet print head to place binder precisely on the powder bed. Another process, 3DEO’s Intelligent Layering, sprays binder over the powder bed and then machines each layer to create the green part with CNC precision. Via such processes, part cost of metal 3D printing lowers to the point where it can compete directly with MIM.
While bind-and-sinter technologies drive down the price-per-part for metal AM, how do they compare to MIM? The best bind-and-sinter technologies today represent an excellent option when on volumes well above prototyping but below the break-even cost of investing in MIM tooling. This decision partially depends on the cost of the mold and when production volumes head north of 20,000 to 30,000 pieces/yr. At volumes just below that, manufacturing via bind-and-sinter technologies becomes the cost-effective choice.
And, remember the freedom offered by metal AM with regard to design flexibility. In addition to the ability to create geometries not possible with MIM, updating a design is trivial with metal 3D printing as compared to buying a new mold with every change. Molds also need maintenance at high production volumes and eventually will require repairs or replacement. Manufacturers working on their new products and researching the most cost-effective way to manufacture small and complex parts need to be investigating bind-and-sinter technologies.
See also: 3DEO Inc
Technologies:
Comments
Must be logged in to post a comment. Sign in or Create an Account
There are no comments posted.MetalForming LIVE On the Shop Floor 2024: Part 1 Re...
Wednesday, April 24, 2024
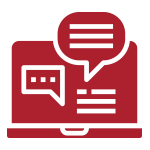

New at EuroBlech 2024: Curated, Guided Visitor Tours
Wednesday, April 24, 2024