During an exclusive 3D Metal Printing tour, we were able to discuss AM in-depth with Sears, and also meet Dr. Ellen Lee, additive manufacturing technical leader for research. And, we took a close look at Ford’s AM development work at the center—including tools, jigs and fixtures; robotic end-of-arm tooling; and production parts—performed on 23 metal and resin machines that employ 10 different AM technologies. On the metals side, the center features a Desktop Metal Studio System (Ford is a Desktop Metal investor) currently running 17-4 stainless steel as well as two SLM Solutions 500 HL units, one running AlSi10Mg aluminum alloy and the other 316L stainless. These represent the first metal-AM machines in Ford’s North American arsenal.
The impressive array of AM-produced products includes the first application off of the SLM stainless-steel machine: a sleeve used on assembly lines to help balance transmissions.
The tool slips over the input shaft of a transmission, allowing a technician to turn the transmission by hand via a ratchet attachment to spin and correctly balance and position the transmission. It’s made of 316L to replace a costly machined predecessor that required extensive lead time.
“These sleeves were made of a hardened tool steel and making them via 3D printing, we were concerned about the interior splines failing,” explains Brad Van Dike, Ford metal additive manufacturing specialist and responsible for the SLM machines at the center. “The AM material, 316L, is one of the softest stainless steels—kind of gummy. Rather than just making one, we made several in case the splines began wearing, and design and build took only about four weeks. Assembly workers only needed one sleeve to turn 100 transmissions, so it has worked out very well.”
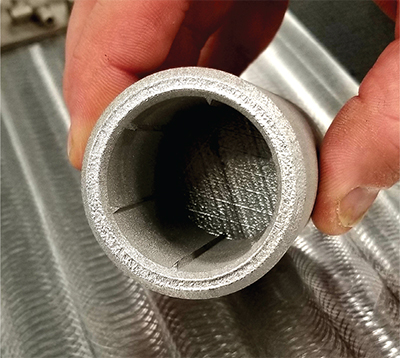
|
The tool sleeve for balancing transmissions was made of a hardened tool steel “and making them via 3D printing, we were concerned about the interior splines failing,” explains Brad Van Dike, metal additive manufacturing specialist at Ford’s Advanced Manufacturing Center. “Rather than just making one, we made several in case the splines began wearing, and design and build took only about four weeks. Assembly workers only needed one to turn 100 transmissions, so the new tool has worked out very well.”
|
Lead time and cost savings peg the tool as an AM winner for Ford. And the wins don’t end there, as the redesign of a transmission-case gripper shows. Fitted on a robot arm, the lift-assist gripper proved unwieldy for assembly personnel and couldn’t adjust to handle larger transmissions. A redesign for AM made it more functional and also delivered almost a tree-branch appearance. The prototype has been printed in plastic and currently is under testing to validate its fit on the line. Once validated, the gripper will be produced in four or five pieces via the Desktop Metal printer, as opposed to perhaps 30-plus parts welded together using traditional manufacturing. And, the new AM gripper will allow for use of the same transmission pallets on the same line. Otherwise, Ford would need to buy new pallets and build a line extension, according to Sears, who estimates that the AM gripper can save Ford as much as $2 million.
“We’re excited about this design and excited about the opportunity to save the company some money,” he says.
Resin Printing Lends Significant Support
The resin machines have helped immensely with prototyping, according to Sears, noting Ford’s stake in AM dating to its incorporation of the stereolithography equipment a quarter-century ago. Today, resin parts, produced at the center on machines from Carbon, HP, Voxeljet, EOS, Prodways, Stratasys and 3D Systems, find their way into numerous prototyping and assembly operations.
“Normally, we store wear tools in warehouse space, but to reduce inventory we are printing those as needed,” Sears explains as he provides more resin-AM manufacturing-support successes.
These include a tool to install O-rings on a transmission input shaft. Ford redesigned the original, a heavy, metal tool with a $900 machining price tag, and printed a new lighter tool for only $70. Sears recalls another case where an engineer needed to mount a laptop on an automatically guided vehicle. Using software, Ford employees designed a bracket within a half hour, and printed and installed it by the next day—impossible with conventional processes, Sears notes.
Success with AM Production
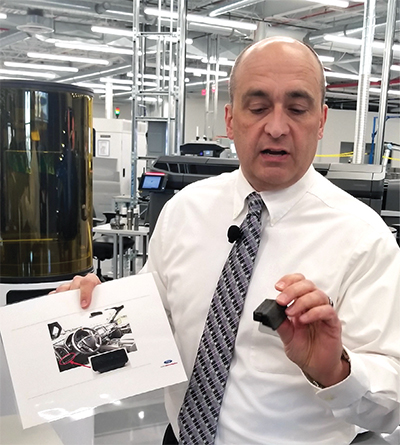
|
Ford’s very first production part, shown by Harold Sears, additive manufacturing technical leader for manufacturing at Ford Motor Co.’s Advanced Manufacturing Center, is a near-automotive-grade-plastic plug that inserts into the instrument panel for Ford Raptors destined for China. A dedicated machine at Ford prints 12 plugs in 1.5 hr., which works well now given the low current volumes.
|
Significantly, AM parts have entered Ford’s production arena. Ford’s very first AM production part: a near-automotive-grade-plastic plug that inserts into the instrument panel of Ford Raptors destined for China. A dedicated machine at Ford prints 12 plugs in 1.5 hr., which works well now given the low current volumes.
The Ford Ranger program also benefits from the company’s AM efforts. Besides the transmission-case gripper mentioned above, four other AM applications support Ranger production, according to Sears. One, a rubberized tool used on the assembly line to set a gap between the Ranger cab and the box, was created and implemented on a Friday after the AM team received a request on the previous Monday—an extremely rapid turnaround.
Another AM production part: a brake bracket that replaces two left- and right-hand brackets for the Ford Mustang Shelby GT 500, unveiled at the Detroit Auto Show this past January.
“Via AM, we redesigned the brackets as a single bracket, which means a lot to us,” Sears says. “We achieved significant time and cost savings while proving the processes, the machines and the part as viable.”
Ford also employs AM for replacement parts in older vehicles, including a heater-control lever Sears displayed.
“We worked directly with our engineers to qualify it, and with very low inventory on that part, we can print it as needed,” he says.
Aggressive 3D Printing Roadmap
As these examples show, manufacturing-center staff employ the resin and metal printers to develop and produce tools, fixtures and jigs to support Ford’s manufacturing environment, and are making inroads into production parts.
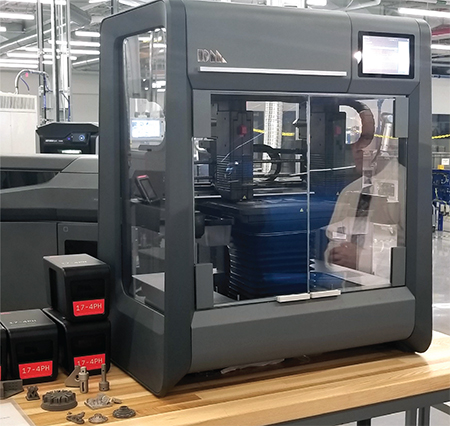
|
Ford performs AM development work—including tools, jigs and fixtures; robotic end-of-arm tooling; and production parts—on 23 metal and resin machines at the center. Metal printers include this Desktop Metal extrusion system running 17-4 stainless steel as well as two selective laser melting units, one running AlSi10Mg aluminum alloy and the other 316L stainless. These represent the first metal-AM machines in Ford’s North American arsenal.
|
“We additively produce tens of thousands of parts per year, primarily to support prototype operations, and now focus a lot more on integrating this technology into the manufacturing space,” says Sears.
In doing so, Ford’s efforts revolve around the following three responsibilities, Sears explains:
1. “How do we use these technologies to make our manufacturing operations more efficient? Can we take costs out of tooling; can we take time out of making the tooling; can we make it more ergonomically friendly for our operators and make their jobs easier?
2. “As we move forward in production, we want to develop AM technology so that we can be manufacturing ready and move it into the volumes needed to support what we do.
3. “We want to be a leader in the industry as far as pushing the technologies to where we want them to go. How do we employ these technologies to benefit our manufacturing system? We want higher speeds and better material properties.”
Prior to the center’s opening, Ford had been pursuing 3D printing in different pockets of the organization, in different areas of manufacturing and engineering, according to Sears.
“We developed the Advanced Manufacturing Center to bring all the focus groups and subject-matter experts together, to benefit from synergies and couple that with robot and machine-vision experts,” he says. “The center brings all of this together to help explore those three responsibilities I mentioned, and help Ford function more efficiently.”
Technology Partners Needed to Reach Goals
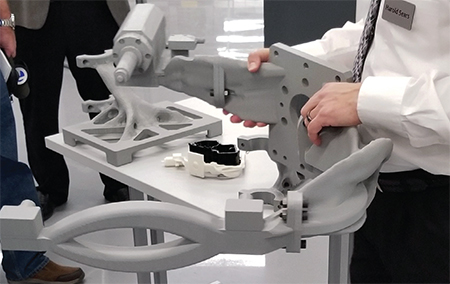
|
Fitted on a robot arm, a lift-assist transmission-case gripper proved unwieldy for assembly personnel and couldn’t adjust to handle larger transmissions. A redesign for AM made it much more functional and also delivered almost a tree-branch appearance. The prototype, shown here, has been printed in plastic and currently is under testing to validate its fit on the line. Once validated, the gripper will be produced in four or five pieces via a metal printer, as opposed to perhaps 30-plus parts welded together using traditional manufacturing. Officials estimate that the new gripper design will save Ford as much as $2 million.
|
“We call our AM machine and technology suppliers ‘partners,’” says Sears, noting that some machines are at the center on consignment and that the company continuously evaluates the technology. “We need the flexibility to do what we need to do, when we need to do it. We work with engineers all over the world, and want a suite of solutions that allows us to zero in and solve some of their problems.”
Toward that end, Sears does not expect Ford to invest in materials and machines and then have providers walk away.
“As we develop relationships, it is important that we understand the technology roadmap of the technology suppliers just as they should understand ours,” he says. “If I think a part could be a great high-volume-production opportunity but I know that the technology is not there today, can the supplier say that in three years or so the challenge will be addressed based on the supplier’s technology growth curves? A prototype application today may not become a production application for three or four years. To reach that point, we need to understand the technology curve. That’s true for machines and materials.
“We want to say that we need build sizes that are about X by X by X, and are looking at this kind of material, and we need production rates of X number of parts per day,” Sears continues. “If a supplier can get there, then we have applications to work on together. This helps suppliers as well. Now they understand the space that we occupy, and where we both need to go. To me, a little information sharing helps both sides.”
The same holds true for Ford’s tier suppliers, and the automaker works closely with part and systems suppliers on applications where 3D printing might work. In fact, the transmission lift-assist gripper described above resulted from a project with a Tier-One supplier.
“Right now we are reaching out to key suppliers on a few programs, considering tool redesigns with 3D printing in mind,” Sears offers. “We want to open their eyes to this, and work with them if they’ll work with us.”
Inhouse Buy-In Progressing
Just like technology partners, Ford needs inhouse buy-in to ensure a path to AM success.
“The momentum has started,” Sears says, “and this includes our UAW workforce.”
Ford installed a polymer printer in its UAW training center, and all new UAW skilled trade apprentices take a 3D-printing course where they learn basic CAD and printer operations. At the same time, the same printer model and technology from the training center has been installed in more than 25 Ford manufacturing facilities globally. These printers are a shared resource for both the salaried and UAW workforces. To help increase awareness and excitement, Ford recently held an internal AM-design and-build competition, with the winner receiving free NASCAR race tickets, including pit passes and the opportunity to meet drivers. The contest resulted in many “incredible” submissions, according to Sears.
“By and large, the effort has been successful,” he says. “Someday we will undertake higher-volume production with this technology, which will require a different skillset for employees across Ford, both hourly and salaried. It’s not about replacing a skilled tradesperson with a machine that prints manufacturing details, it is about giving skilled tradespeople new methods to do things faster and more affordably. We see some skilled tradespeople jumping onboard and doing incredible things—taking the basic training and going further by teaching themselves more advanced CAD techniques and exploring new use cases for the technology. We need that enthusiasm, and we need the right environment for it to take hold and we are making great progress on both fronts.”
Besides an increase in employee skillsets, Ford’s 3D printing path also targets employee wellbeing.
“Suppose a technician handles a 5 or 7-lb. tool on the assembly line,” Sears explains. “A vehicle leaves that line about once per min., so that tool may be handled hundreds of times per day. What if we redesign that tool and reduce its weight to 2 lb.? We’re doing that. Our engineers take to the floor almost as evangelists for the technology, asking questions and looking for solutions to make the job better for everyone.”
Bottom line: Successful AM integration requires a new way of thinking.
“An engineer might come to us with a stamped production part and wonder what it would cost to 3D print,” says Sears. “We won’t go there, as 3D printing loses the battle every time. That part was designed to be stamped. Instead, we try to have our associates look at a part and see what it does—the part’s function, the pieces it connects to, and the part’s entire system. Can the system be redesigned for 3D printing? It’s all about opening up to more creative designs and more efficiency, and designing systems for what they need to do, not for manufacturability. 3D printing provides that ability.”
It’s safe to say that Ford is on board with AM, and, if Sears’ prior experience is any indication, its adoption by the automaker will only grow.
“Twenty-five years ago, as a CAD specialist at Ford, I saw the new stereolithography machine and started asking questions, and told my supervisor that I wanted to be working with that,” he recalls. “They let me move, and we literally wore down that one machine. My first expansion project with the technology took us from that one machine to five, and within six months we reached capacity on those five machines. My boss told me that I was supposed to look to the future when I planned that expansion...I thought I did!
“But now we are on the fourth expansion with this technology,” Sears concludes. “Every time I thought we overdid it, but we haven’t yet. 3D printing just keeps growing at Ford.” 3DMP
Industry-Related Terms: Prototype,
Stainless Steel,
Aluminum Alloy,
CAD,
Case,
Center,
LASER,
Lead Time,
Lines,
Manufacturability,
ModelView Glossary of Metalforming Terms
See also: Desktop Metal, Inc., SLM Solutions NA, Inc.
Technologies: