“It's just a huge aid to have in our tool shop, especially when we get really busy,” he says.
Another time-saving example involves a large mold that required 12 inserts, each with a different design. Without metal AM, “we would have had to set up and EDM each of these insert areas one at a time,” explains Staub. Using metal AM, BasTech built all of the inserts, in one run, over a weekend. “It was a huge time saver,” he says. “And it is a lot easier to manage and schedule one automated operation than a five-step process repeated 12 times.”
Staub also finds that metal AM reduces the possibilities for human error to derail a project.
“There is no perfection in a tool shop,” he says. “Human error can occur in every step of the process.”
While metal AM isn’t immune to human error, it reduces the number of touch points, which reduces the frequency of unpleasant surprises.
“I have a totally optimistic view of 3D metal printing. Yes, there are challenges, and I think those challenges should be considered. But it’s important to adopt an open-minded approach and ask how the challenges can be overcome,” says Ben Staub, founder and president of BasTech, Inc.
|
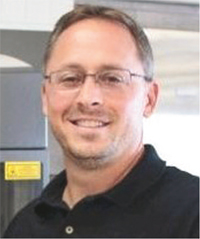
|
Sticking with toolmaking, Staub’s final example of open-minded thinking focuses on the concept of conformal cooling, where cooling channels snake through an insert rather than running along straight lines. Conformal cooling often is touted as, and perceived to be, a cycle-time reducer in the injection-molding press. This is a unique benefit, but not the sole advantage in Staub’s shop.
“We have applications where we use conformal cooling to produce better parts,” Staub says. “For example, we mold 300 to 500 of a certain paintball-gun component per week. Conformal cooling knocks off about 8 sec. per shot, which saves us about 45 min./week on the press. That didn’t justify the cost of printing this tool. With metal AM, we can move water to places that wouldn’t be possible without conformal cooling. That allows us, using metal AM, to mold a flat part.”
Optimistic and Enthusiastic
“I have a totally optimistic view of 3D metal printing,” says Staub. “Yes, there are challenges, and I think those challenges should be considered. But it’s important to adopt an open-minded approach and ask how the challenges can be overcome.”
A critical factor is accepting that metal AM can be used when it makes sense.
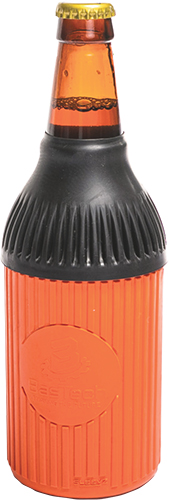
|
Metal AM can eliminate a large amount of shop time and circumvent the shortage of qualified labor when, for example, producing a core with complicated geometry, such as for this molded bottle sleeve. In such cases, EDM work may require a five-step process: design the electrodes, program machining of the electrodes, cut the electrodes, set up the EDM and then burn the core. Using metal AM, the BasTech team can program a metal-AM machine and let the core build over a weekend, accelerating the process and freeing employees for other work. |
“It's really no different than any other tool in the shop,” Staub explains. “Without metal AM, machinists select the right machine tool for the job. Most people have multiple mills–some are high speed, some are large, some may strictly set up for cavities and others strictly for cutting electrodes.”
Metal AM doesn’t replace all of this equipment. Instead, it should be added to the list of tools considered for the job and used when it makes sense.
“I'm just thrilled to death to be in this market because I can do things now that I couldn’t do a couple of years ago,” Staub concludes. “Even though adoption is slower than I would like, it is moving. Metal AM is an incredible market, and has become a vital part of what we do at BasTech.”
Commentary
From Staub’s insights, and from those offered in previous editions of Grimm’s 3D Metal Printing Tales, it is obvious that the human mind represents a significant barrier to metal-AM adoption. Yes, the technology isn’t perfect, but this observation only serves as a logical rationale to a more emotional, gut-level decision. The ‘facts,’ such as looser tolerances than those for machining, become the evidence that supports a decision to remain status-quo. These ‘facts’ prevent many from enjoying the unique advantages of metal AM.
BasTech’s Metal-AM Portfolio
DMP Equipment
- 3D Systems ProX DMP 100, 200 and 300
Materials
- Maraging steel
- Aluminum (AlSi12)
- Nickel alloy (Inconel 718)
- Stainless steel (316L, 17-4PH)
- Also provides materials development
|
Open-mindedness isn’t just a personality trait. It is an aptitude that requires consideration and investigation. It requires effort. Metal AM is similar to traditional processes in many ways, yet distinctly different in many others. Willingness to open one’s mind is just the start. That must be followed by a thorough inquiry that reveals both the differences and the similarities. Only then can potential users make informed decisions as to when metal AM makes sense.
Becoming informed takes time. Whether or not you believe that metal AM is real today, it is time to start the investigation so that you are prepared to act when the opportunity presents itself. 3DMP
Have a difference of opinion or insights that you would like to share? Contact Brad Kuvin (bkuvin@pma.org), editor, to schedule an interview.
Technologies: