Manufacturer's Cost-Effective Versatility
June 1, 2014 ...is fueled by abrasive waterjet cutting, so much so that a second waterjet machine may soon be on the horizon.
As the first of four very successful enterprises, West Coast Steel Fabricators, Eugene, OR, launched operations in 1979 as a custom fabricator of conveyors, bins, hoppers, tanks, trusses, ductwork, silos and more. Today, the 50-person shop, under the direction of owner Brian Hough, also provides fabricating expertise and capabilities to its three operating divisions—Olympus Technologies, Inc. (OTI), Olympus Trailers and Cascade Truck Body & Trailer Sales. OTI manufactures equipment for wastewater-treatment facilities; Olympus Trailers builds large motorsports and utility trailers; and Cascade Truck Body & Trailer Sales up-fits trucks for service and heavy-duty industrial use. What these divisions, as well as West Coast Steel Fabricators, have in common is that they all benefit from cost-effective, highly versatile waterjet cutting.
Diversify, and Elevate Quality
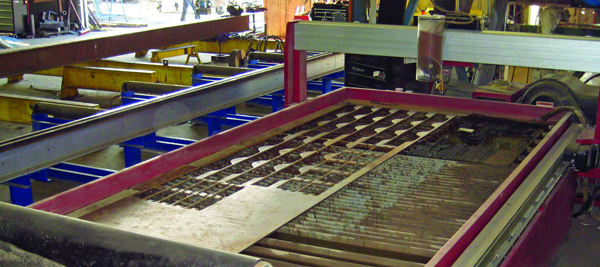 |
The Maxiem 1530 JetCutting Center at West Coast Steel Fabricators produces parts that are beautifully finished right off the machine. It has eliminated as much as 2 hr. of finishing time from most parts, as well as the man-hours usually spent deburring and cleaning. |
A few years ago, Hough looked to expand and diversify his business in the face of the new economic reality. He wanted to expand his custom steel product offerings and elevate component quality to higher levels. That’s when he turned to abrasive waterjet cutting to handle a wider range of production runs, including fast prototype development. The shop now can quickly turn around highly accurate parts without the hassle of tool changes or complex fixturing. Plus, as compared with other production equipment in the shop, abrasive waterjet cutting generates smoother surface finishes, Hough says, which often can eliminate the need for secondary machining.
Hough’s machine of choice: a Maxiem 1530 JetCutting Center from Omax Corp., with an x-y cutting travel of 122 by 62 in.
According to Hough, once the machine landed in his shop only a few hours of employee training—on the machine and on the Omax Intelli-Max software—were required to launch production.
“I had long been interested in waterjet cutting,” says Hough, “so when I was ready I contacted Omax, nearby in Kent, WA. Once I decided on a machine model, Omax had it here within three days. On delivery day, we were up and running.”
Where the Maxiem 1530 really shines, says Hough: producing parts that are beautifully finished right off the machine. It has eliminated as much as 2 hr. of finishing time from most parts, as well as the man-hours usually spent deburring and cleaning.
Life Before Waterjet
Prior to waterjet cutting, Hough’s businesses had relied on high-definition plasma cutting of parts. And while that process still accounts for a large amount of his daily operations, it cannot compete with the waterjet in terms of accuracy, especially when cutting the shop’s aluminum and mild- and stainless-steel plate.
“With our high-def plasma, we can get speed but not accuracy,” Hough says. “Parts come off the plasma-cutting machine and must be polished, the edges cleaned up and a reamer run through the holes. These operations add up to an extra 90 min. of time tacked on to every part.
“With the waterjet,” Hough continues, “we can cut the same number of parts as with plasma, but when the waterjet parts are done they are ready to ship. In fact, we now have internal guidelines noting certain parts only can be produced using the waterjet machine—specifically, those parts that will be customer-facing. We want to show off these parts, which give the equipment a high-tech look and feel. Parts are cut perfectly and look beautiful every time.”
Accessorized, for Cutting Uneven Surfaces
Recently, the shop added the Omax Collision Sensing Terrain Follower accessory to its cutting machine, which contends with cutting uneven part surfaces. The accessory has proved particularly useful for cutting parts for OTI—Hough’s anaerobic digestion-equipment division. Prior to adding the Terrain Follower, when the waterjet-cutting head would encounter an uneven surface, the machine would automatically shut off.
“Initially, we did not realize the need for the Terrain Follower,” recalls Hough. “Fortunately, we were able to retrofit the device to our machine. Now, if our plate stock has a bit of a wave to it, the machine just follows along seamlessly and without any issues or special programming.”
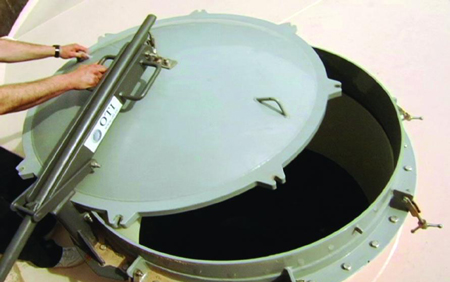 |
Recently, the shop added the Omax Collision Sensing Terrain Follower accessory to its waterjet-cutting machine, which contends with cutting uneven part surfaces. The accessory has proved particularly useful for cutting parts (shown here) for OTI—Hough’s anaerobic digestion-equipment division. Prior to adding the Terrain Follower, when the waterjet-cutting head would encounter an uneven surface, the machine would automatically shut off. |
In addition to OTI, Hough’s Olympus Trailers division, in particular, leverages the unique capabilities of waterjet cutting. Its high-end trailers feature extensive aluminum constructions, including all-aluminum-framed cabinets with stainless-steel countertops in work areas and heavy-duty aluminum doors.
In the shop, Hough’s employees frequently experiment with new applications for the waterjet-cutting machine. They now cut practically any type of material, including rubber, thermoplastic polyethylene, aluminum, stainless steel and carbon fiber.
“We even cut the wood for our skids with the waterjet,” says Hough. “All of our equipment ships out on wood skids, which require cutting prior to shipping. Thanks to one of our experiments, we recently switched to making those cuts with the waterjet. As a result, we took a job that previously took 7 to 10 hr. to run and finished it in 3 hr. Now that we can complete that job so quickly, we have time to cut our company logo into the pallets, which we had never done before.”