Waterjet Makes the Cut for Architectural Customers
November 1, 2019 Commercial-architectural customers set the bar
for custom fabricated jobs. Waterjet cutting delivers.
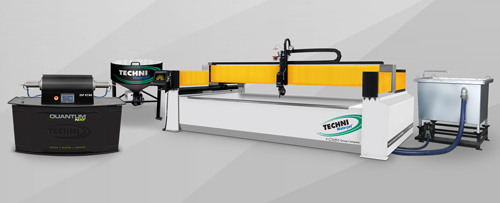
|
Waterjet cutting equipment at Captive Spark, a California custom-fabrication shop, enables precision-cut architectural panels, often within tolerances of ±0.005-in. |
Captive Spark, a custom-fabrication shop in Berkeley, CA, serves a finicky customer base requiring precision cutting, with expectations running high when it comes to aesthetics.
“Ninety percent of our work is for tech firms such as Dropbox, Amazon and Google,” says Alex Frith, owner of Captive Spark, a four-person operation. The company launched in 2001 as a one-person shop with “low-end welding equipment and a combination lathe/mill machine in a 1500-sq.-ft. space” where Frith modified road-racing motorcycles. As the company gained larger jobs, it added a plasma cutter but made the switch to waterjet cutting this summer when it installed an Intec-G2 waterjet cutting machine from Techni Waterjet, Charlotte, NC. Today the plasma-cutting equipment is used for projects that don’t call for tight tolerances, such as custom-railing and public-art projects.
“We’re using the waterjet for labor-intensive architectural metal (stainless, brass and copper) components such as custom reception desks and cladding for wood cabinets,” Frith says. “While we’re not making aerospace parts, we are producing sheet metal formed parts where ±0.005-in. tolerances are critical. If the flat pan isn’t accurate, neither will be the sides.
“The waterjet, a 5- by 10-ft. machine, makes for a small footprint, Frith continues. “The servo pump is efficient and its Tech-Sense feature monitors the cutting head and pauses the program if there are blockage issues, allowing us to run the machine unattended.”
Good Business
One reason for moving toward waterjet cutting, according to Frith, is that it made good business sense. “Low operational cost, lower maintenance cost and lower labor cost all equal more profit for the shop,” says Jim Fields, national sales manager at Techni Waterjet.
Frith concurs. “We had been outsourcing a lot of our jobs to shops with laser-cutting equipment,” he says. “With the waterjet, we were able to move those jobs inhouse, and the equipment is less expensive than a laser. We also like that the waterjet cuts plastic and rubber as well as metals.”
Another plus: a gentle learning curve. “With plasma, there’s a bit of voodoo associated with the technology,” says Frith. That is, the plasma arc changes in size and shape depending on such variables as amperage, voltage, gas flow and velocity of the moving torch, As the plasma-arc column changes, so does the amount of metal removed by the plasma arc.