Because some aluminum alloys are more susceptible to cracking than others, it’s important to select a filler metal that will result in weldmetal composition with low crack sensitivity. When welding aluminum that has low crack sensitivity, als use a filler metal of similar composition. Conversely, when welding aluminum with high crack sensitivity, select a filler metal with a different composition that will deposit a weld with low crack sensitivity.
Aluminum filler metals are identified by a numerical American Welding Society (AWS) classification that corresponds to the Aluminum Association registration number identifying the particular alloy composition. Not all filler metals are suitable for welding all aluminum base alloys. Reference a reputable filler-metal selection guide to make the best choice for welding different aluminum alloys.
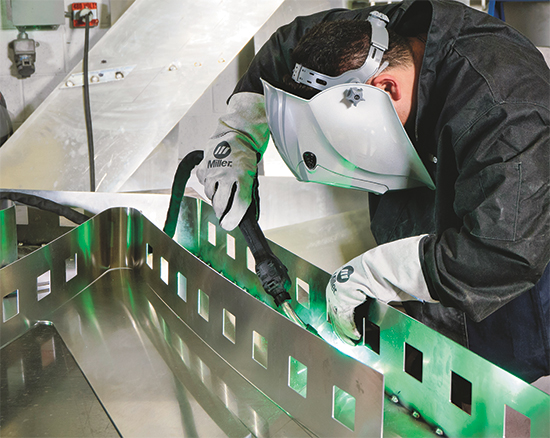 |
While cracking is one of the most critical issues that can occur with aluminum weldments, most aluminum alloys can be successfully welded without cracking-related problems. Using the most appropriate filler metal and completing the weld with the appropriate procedure will help ensure success. |
Weld-joint design is another important consideration that affects the composition of the weld, and therefore can help prevent hot cracking. A weld joint with no bevel can result in inadequate base-metal dilution, while a weld joint with an appropriate bevel results in adequate dilution. This means a beveled edge can increase the amount of filler metal deposited in the weld, producing a composition less likely to crack. With some aluminum base alloys, such as the 6xxx series, this is a very important factor that can strongly influence the likelihood of hot cracking.
Stress Cracking
While not as common as hot cracking, stress cracking also can affect aluminum welds. A primary cause of stress cracking: excessive shrinkage rates during weld solidification and cooling. Selecting a filler metal containing silicon, when appropriate, can reduce shrinkage stresses to help avoid stress cracks.
Most cracks in aluminum welds appear in the crater (defined as an undesirable depression in the weld bead), and often go unnoticed. While crater cracks start small, if not addressed they can propagate throughout the weld and cause major failures. As a best practice, welders should take care to completely fill the crater during welding, either by using an automated crater-fill function on the welding power supply or by using some other approved method of filling the crater.
Increasing weld-travel speed can help reduce the probability of stress cracking, because it narrows the heat-affected zone and minimizes base-metal melting. Preheating also may help, by reducing residual stress levels of the base material during and after welding. This in turn will lower the probability of stress cracking.
Avoid welding aluminum that is very cold, and avoid overheating during preheating operation—a 150 F preheat temperature suffices for all aluminum alloys. Overheating some alloys, such as those in the 6xxx series, can unacceptably reduce base-material tensile strength.
Weld-Joint Porosity
While not as critical of an issue as cracking, porosity is perhaps the most common complaint when mig welding aluminum. Porosity refers to the cavity-like discontinuities in the weld formed by gas entrapment during solidification.
Weld porosity results primarily from the absorption of hydrogen during melting and the expulsion of hydrogen during weld-pool solidification. Sources of hydrogen that create porosity:
• Hydrocarbons, in the form of paint, oil, grease and other lubricants and contaminants.
• Hydrated aluminum oxide—aluminum oxide that has absorbed moisture can release hydrogen when subjected to heat during the welding operation.
• Moisture, which can come from the atmosphere (humidity) or from other sources such as compressed air, small leaks in water-cooled torches, contaminated shielding gas or precleaning operations.
The first step in solving this issue: Identify the source of hydrogen responsible for producing the porosity. Weld shops also can purchase low-dew-point shielding gases (argon or argon/helium mixtures) to help reduce weld porosity. And, ensure welders closely follow the recommended shielding-gas flow rates and purge cycles for the welding procedure and weld position being used.
Welding operators must thoroughly clean base metals with a solvent and clean cloth or paper towel, followed by stainless-steel wire brushing prior to assembling the weld joint. Note: Shop rags typically are not clean enough for use on aluminum, as they can contain residual hydrocarbons that contribute to porosity.
Also, ensure that the base metal and filler metal are condensation-free. When bringing aluminum in from a cooler location (such as outdoors), allow it to sit in the welding area for 24 hr. before welding. Likewise, store unpackaged aluminum filler metals in a heated cabinet or room to help prevent them from cycling through dew points and avoid creating hydrated oxide on their surface.
Lastly, diligently purchase high-quality filler metals from reputable manufacturers. Such filler metals typically have been diamond-shaved to eliminate harmful oxides; manufactured following procedures to produce low residual-hydrogen-containing compounds; and weld-tested to stringent AWS standards.
Prevent Erratic Wire Feeding and Unstable Arcs
Welders can follow several guidelines to avoid erratic wire feeding and arc issues, starting with using a welding power supply and consumables designed specifically for aluminum. Use the right kind of contact tips, with the size matched to the wire diameter being used. And, use a contact tip designed for aluminum wire; using a tip designed for steel wire can cause excessive burnback when welding aluminum.
The contact tip should be recessed in the gas cup by 1⁄8 to ¼ in. to ensure proper gas cooling of the tip, and for spatter control. As the contact tip wears, arc flaring can become a problem. To prevent this, replace contact tips as needed.
Selecting the correct type of drive roll will help to prevent wire-feeding issues when delivering aluminum weld wire to the joint. The majority of these problems result from aluminum wire shavings that originate from poor fitting and incorrectly designed drive rolls. The shavings can build up and clog the weld-gun liners, restricting the free flow of the wire. Use a U-groove drive roll in the wire feeder, designed for aluminum; a V-groove drive roll will compress the wire and deform it, causing erratic arc conditions.
Also, carefully align the drive rolls, and als use the lowest drive-roll pressure capable of consistently feeding the wire. Performing regular maintenance and periodically replacing items that wear, including drive rolls, liners and inlet guides, also helps prevent wire-feeding issues. Use a push-pull wire feeder or spool gun to promote optimum wire feedability. Most push-pull guns have two liners: a conduit liner, which typically lasts longer, and a head-tube liner in the gun portion, which can wear out more quickly. Periodic replacement of both liners proves helpful, especially once clogging becomes an issue.
Minimizing Weld Discoloration and Smut
Introduction of oxygen into the shielding-gas envelope via air, moisture and contaminants can increase burning (oxidation) of the filler metal, which produces weld discoloration and smut. The use of certain filler metals also can contribute to this problem.
While weld discoloration and smut look bad, they are easy issues to avoid. The 4xxx series of filler metals produce less weld discoloration and smut than do the 5xxx series—magnesium in 5xxx-series alloys vaporizes in the arc and condenses as black soot next to the weld bead. Most 4xxx-series alloys contain little or no magnesium. Also, welders can keep air out of the shielding gas by decreasing welding-gun angle, increasing gas-cup size, holding the gas cup closer to the base metal, removing spatter buildup from the gas cup and carefully shielding the arc from drafts. Welders used to working with steel may be dragging their weld. Use a push angle instead, to put the arc-cleaning action in front of the weld. This angle continually cleans the weld and reduces smut. MF
See also: Hobart Brothers Co.
Technologies: Materials, Welding and Joining