Welding: How to Choose the Right Solid Wire
June 1, 2016 Solid wire is simple to use, making it a popular
choice across welding applications. But given specific materials and applications, which wire is best? Read on to find out.
No two welding operations are the same. Yet in many cases, companies come to rely on similar filler metals to get the job done. Solid wire is among the most widely used filler metals in the industry and is a common choice for applications ranging from general fabrication and manufacturing to maintenance/repair and pipeline welding.
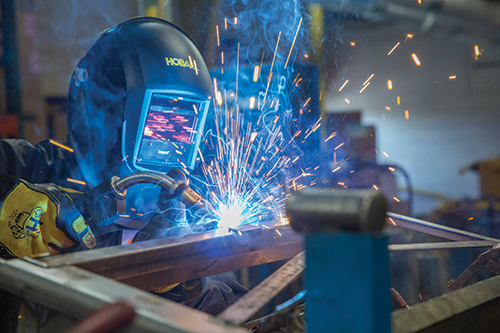 |
Solid wire is one of the most-used filler metals in the welding industry the world over, and is a common choice for applications ranging from home hobbyists to general maintenance to repair. It can be used to weld many types and thicknesses of materials, from very thin alloys to thick structural metals for steel buildings. |
The wire’s ease of use contributes to its popularity, as does its ability to weld many types and thicknesses of materials. Welding technology available on the market today also makes it easier for welding operators of varying skill sets to create quality welds with solid wire.
As with any type of filler metal, keep in mind several considerations when choosing a specific solid wire for an application. Different classifications offer varying characteristics for each solid wire, all of which can impact weld strength and quality, as well as the amount of post-weld cleanup needed.
Solid Wire: An Overview
The American Welding Society (AWS) provides multiple classifications for solid wire based on the mechanical and chemical properties each provides. Each letter and number in its nomenclature signifies a specific feature. As an example, for a commonly used solid wire, AWS ER70S-6, the “ER” indicates that the filler metal is an electrode or rod; the “70” signifies that it has a tensile strength of 70,000 lb./sq. in. (psi); and the “S” means that it is a solid wire. The “6” reflects the chemical composition and shielding gas requirements.
Solid wires with “S-3” and “S-6” suffixes are among the most commonly used in the industry for gas-metal-arc welding (GMAW). For gas-tungsten-arc welding (GTAW) applications, an ER70S-2 cut-length (or rod) often is used.
Solid wires are available in a range of diameters. For GMAW, diameters range from 0.023 to 1⁄16 in., whereas solid wires used in submerged arc welding (SAW) can have diameters to 1⁄8 in. and larger. GTAW cut-lengths are available in diameters of 1⁄16 to 5⁄32 in. Typical operating parameters for solid wire depend upon these diameters and, for GMAW or SAW, also on wire-feed speed. Wire-feed speed is proportional to the amperage used for the welding application. Voltage can range from 14 to more than 30 V.
When using solid wires, spray transfer and short-circuit transfer are two common welding modes. The transfer mode used for an application depends upon the shielding gas and the welding parameters. To achieve spray-transfer mode requires a minimum of 85 percent argon in the shielding-gas mixture. The result of this mixture is less undercutting and a more fluid, controllable puddle. The preferred gas for short-circuiting transfer mode is 75-percent argon/25-percent CO2, which provides good arc transfer, lower levels of spatter and a nice appearance of the completed weld bead.
Common Types of Solid Wire
Each classification of solid wire has unique benefits, limitations and best uses. Following are some common types of solid wires, along with their attributes.
AWS ER70S-6
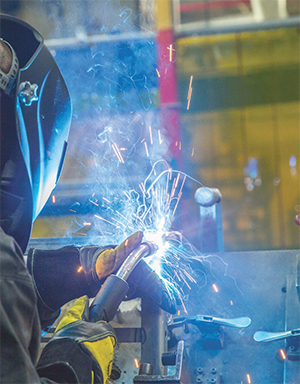 |
When welding on clean base material, solid-wire filler metals deposit very little slag, resulting in minimal post-weld cleanup. Because of this, solid wire commonly finds use for tack welding or other applications where a clean surface is important. |
An ER70S-6 solid wire is the most common choice for welding mild steel. This widely available wire is found in general fabrication and automotive-welding applications, and can be used for robotic welding as well as to complete root passes for pipe welding and other critical or industrial applications. It offers smooth and consistent wire feeding, which helps support greater productivity (less downtime to address feeding issues), and the wire helps increase consumable life. With proper use, it creates smooth weld beads with uniform tie-in.
Welding operators can use ER70S-6 solid wire with 100-percent CO2 to increase joint penetration or with an argon/CO2 blend to help minimize spatter. Note that these wires tend to generate silicon island deposits on the surface of the completed weld. Operators must remove these deposits prior to painting or other types of surface conditioning, which may increase time required for post-weld cleaning.
While solid wires generally generate low spatter levels on clean base materials, they may not be the best option for welding contaminated metals. If, however, there is no alternative, an ER70S-6 wire may be helpful for welding through light rust or mill scale. This wire has greater percentages of silicon and manganese, which act as excellent deoxidizers.
AWS ER70S-3
ER70S-3 solid wire is another common choice, used primarily in applications where a clean finished weld is important. Similar to an ER70S-6 product, this wire provides good wire feeding, but it also generates a clean weld deposit that can be ready to paint or plate with little post-weld cleaning. It’s a common choice for automotive and automated welding as well as general fabrication, light sheetmetal fabrication and in applications requiring high wire-feed speeds.
Also like an ER70S-6, this wire can be used with 100-percent CO2 or with an argon/CO2 mix, depending upon whether greater joint penetration or low spatter is the desired outcome.