“A number of factors need to be considered when recommending a metalforming fluid,” says STLE member John Steigerwald, vice president for business development for Etna Products Inc., in Chagrin Falls, OH. “The key consideration is choosing the proper fluid and applying the proper amount of lubricant in the proper places at the proper time. All of the considerations of the particular metalforming process must be considered when choosing the fluid.”
A metalforming lubricant company must have a thorough understanding of the operation. This includes what happens to the metal part, both before and after the metalforming process. “The metalforming formulator needs to be a knowledgeable process expert who works with a customer to ensure that all items are identified, discussed and understood prior to making a recommendation,” says Steigerwald. “This is not just asking what the customer is using today and coming up with a product to match, because the product used today might not be the best one for overall process needs. Rather, the metalforming lubricant representative needs to be viewed as a technical consultant to provide solutions to the end-user and not just as a lubricant supplier.”
Steigerwald believes that the metalforming industry is looking at changes in lubricant technology to keep up with the process changes end-users are requesting to improve productivity and reduce overall production costs. For example, “The industry continues to seek replacements for the standard phosphorus- and soap-based cold metalforming coatings,” he says. “Among the options is a coating that can be dried and applied without the process steps and waste byproducts that exist today in the phosphorus/soap method or even by using other wet media.”
Changes of this nature not only entail a change in the type of lubricant, but also lead to a change in how the end-user handles the following:
- Process and equipment changes;
- Maintenance procedures;
- Training on the new process and fluid; and
- Pre- and post-issues.
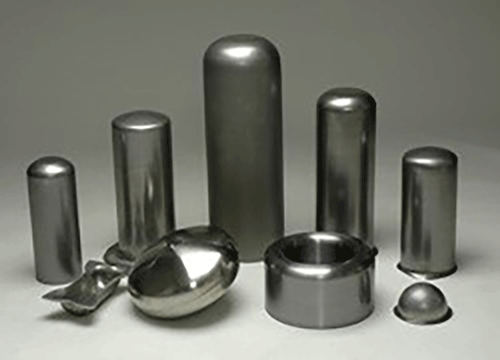
|
Fig. 1—Parts produced by the deep-drawing of metal. This metalforming operation uses a press to draw metal so that the depth of the draw is deeper than the diameter of the punch used. (Courtesy of Etna Products Inc.) |
This is not just a lubricant change but, more comprehensively, a process change that takes a commitment from both the end-user and the lubricant supplier. Change is an asset, but it does not come without the commitment and focus to make it a reality on the part of the stakeholders.
Steigerwald emphasizes that a lubricant supplier must not only know that his product’s capabilities but, more importantly, must have the industry and process knowledge to assist in the challenges faced by customers. Concurrently, the lubricant supplier must bring forth true solutions based on technical and engineering knowledge. These solutions must not be just another “me-to” product answer with a lower acquisition price.
Impact of Lighter Metals
A second factor affecting the types of metalforming fluids used is the greater use of lighter metals such as aluminum, magnesium, magnesium alloys and titanium. Steigerwald attributes this to the need for improving fuel efficiency, conserving energy, improving strength and reducing weight, particularly in the automobile, aerospace/aircraft and energy sectors.
According to Steigerwald, the metalforming lubricant industry must work with end-users in the design, research and development of future processes, not after they are developed. Technical-exchange consortiums involving universities, OEMs, the metals industry, and press and die manufacturers help facilitate stakeholder discussions.
Metalforming Case Study
A case study illustrating these steps concerns an automotive door hardware manufacturer that built a new 14-station progressive die to manufacture a truck tailgate latch. “A series of operations, including an irregular draw, hole punching, notching and extrusion, are planned for a 400-ton Straightside Press,” says Michael Cesa, market development manager for Etna Products, Inc. “A series of operations including an irregular draw, hole punching, notching and extrusion are planned for a 400-ton Straightside Press. The entire process needed to be validated because the die and the entire press line are new.”
Initially, the manufacturer encountered serious wall thinning of the metal during manufacture. “Thinning was as high as 40 percent in some areas, which exceeds the 20-percent acceptability rate requested by this end-user,” says Cesa. “A typical acceptability rate for most applications is 10 percent. The higher acceptability rate for this process is due to its severity.”
The approach taken to reduce the thinning rate was to evaluate the die design through circle-grid analysis. In this process, a series of circular patterns etched on strips of metal placed in a die. Analysis of the local forming patterns enables the degree of thinning to be predicted.
“Circle-grid analysis allowed us to recommend that an additional die station be used and that the clearance between the punch be expanded,” Cesa says. “These options improved the flow of metal, which reduced the degree of metal thinning.”
Based on this analysis, an emulsifiable oil formulated with boundary lubricity and extreme pressure additives was recommended, resulting in improved performance with the thinning rate reduced to acceptable levels.
Deep-Drawing
One particularly challenging metalforming operation, deep-drawing of steel, was singled out by several fluid representatives. Cesa defines deep-drawing as an operation using a press (mechanical or hydraulic) to draw metal so that the depth of the draw is deeper than the diameter of the punch used. Parts prepared from deep-drawing are shown in Fig. 1.
Kathy Helmetag, senior research chemist for Henkel Corp., Madison Heights, MI, explains that deep- drawing leads to an expansion of the surface area of the metal part. “During this process,” she says, “the surface area increases by one to two times the area of the original sheet. An example is making a bathtub out of a sheet of steel.”
The type of metalforming fluid often used in such an application contains extreme-pressure additives. Helmetag terms this ironic because the operation is usually run under hydrodynamic lubrication conditions. The metalforming fluid can have a viscosity of up to approximately 1000 SUS at 40 C. “The metalforming formulator is not necessarily looking for that high a viscosity, but the additives required to achieve the required performance often lead to a relatively viscous fluid,” she says.
Neat oils and emulsifiable fluids are the main types of lubricants used for deep drawing. However, the industry is looking to move away from chlorinated paraffin-based fluids and neat oils for regulatory concerns and cleanability. In the latter case, Helmetag believes this also will improve rust protection on the deep-drawn part and reduce operating costs.
“The lubricant supplier must evaluate the entire metalforming operation and focus on the most difficult part of the draw,” she says. “Specific areas on the die are under very high and constant stress during the deep draw. Steel, that is not deformed properly, could spring back and grab onto the punch.”
Determining which metalforming fluids do not work is as important as understanding what fluids do work. Helmetag believes both aspects need to be understood to optimize the product.
Steigerwald feels that the lubricant formulator must find the ability to balance boundary versus hydrodynamic lubrication. Steigerwald feels that the trend is moving toward emulsifiable oils because of their ability to provide cooling. Chlorinated extreme-pressure additives have been a main component in deep-drawing oils, though chlorine-free technology has been used successfully in the European Union.
Deep-Drawing Case Study
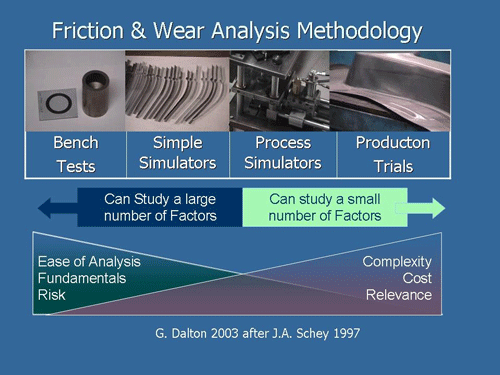
|
Fig. 2—There are distinct differences between using bench and simulation tests to evaluate metalforming lubricants. Bench tests can provide fundamental data that may be pertinent to a specific operation. Simulation tests are more focused on a specific process and cannot be applied to other applications. (Courtesy of TribSys LLC) |
A 0.2-in.-thick grade of high-strength steel sheet underwent a severe deep-drawing operation in the extreme-pressure-lubrication regime. The end-user used a chlorinated paraffin-based emulsifiable oil and wanted to switch to a chlorine-free product.
Helmetag was tasked with determining whether this application could be done without chlorinated paraffin. Initially, fluid candidates were evaluated in the actual operation. “We found out which fluids could stamp out parts and which caused parts to fuse to the die or not fully release from the die,” she says. “Based on the results, we then organized the candidate fluids into ‘go-no/go’ pairs for use in lab testing.”
Fluids designated ‘go’ worked in the application, while those labeled ‘no-go’ failed. To accomplish this task, the end-user must fully engage in the process.
“There are probably 4000 tribotests available for use in evaluating lubricants,” Helmetag says, “particularly when you consider all the variations of each method on each instrument. Our approach was to utilize test methods that can evaluate each metalforming lubricant candidate under elastohydrodynamic, boundary and extreme-pressure lubrication regimes.”
The tests selected were the PCS instrument used to evaluate variable slide-roll contact in the elastohydrodynamic region, the drawbead tester to measure boundary-lubricant characteristics and the four-ball EP tester to evaluate the weld points of these lubricants.
Helmetag found that the four-ball EP weld test could correlate with the ‘go-no/ go’ pairs but could not differentiate the performance of the ‘go’ fluids. “We then captured the run data and were able to evaluate the friction-force curve to determine which of the ‘go’ fluids will work best in the actual application,” she says.
Even then, four to five additional trials were needed to optimize the product, a chlorine-free emulsifiable oil. The chosen deep-drawing fluid is doing well in long-term testing.
“The lubricant formulator needs to go beyond existing laboratory test methods to tailor evaluation procedures so that they can correlate with the specific application,” Helmtag concludes. Evaluation testing also will need to be distinct for each metalforming application because unique tribological conditions are found with every die.”
Friction Testing
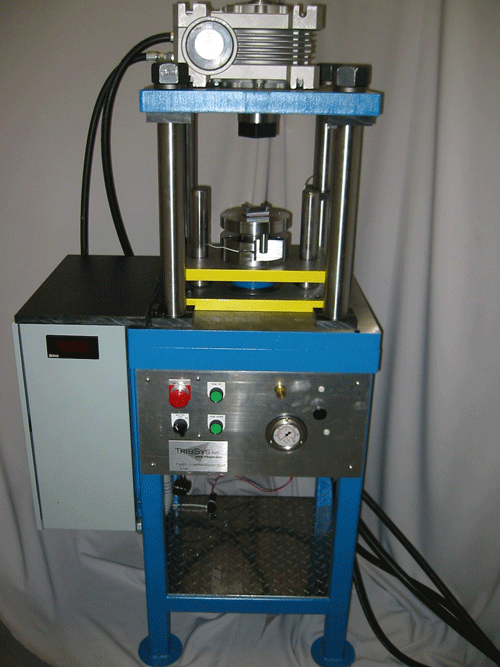
|
Fig. 3—The Twist Compression Tester is a lab-bench test for evaluating lubricant performance over a range of conditions. The transmitted torque between a rotating annual cylinder and a lubricated flat-sheet specimen is measured. (Courtesy of TribSys LLC) |
Testing of metalforming fluids is an important criterion in finding the right product for a specific operation. Ted McClure of TribSys LLC, Valparaiso, IN, says, “In evaluating a sheet metalforming operation, the key parameters to be studied are interactions among the tool, workpiece and the lubricant. These interactions are unusually complex.”
Selection of a test procedure depends on what is being studied. Among the possibilities are lubricants, friction effects and equipment. “A fundamental distinction that people must make when considering which test to use,” McClure says, “is the difference between bench and simulation testing. (Fig. 2 shows the differences between bench and simulation testing.) Careful attention must be paid to the ways that the specific test can be connected with the industrial process being studied.
“Simulation tests can be used to study such parameters as process variables, die radii, materials and surfaces, speeds, lubricants, sheet materials and sheet thickness-to-die clearance ratios,” he continues. “Many simulation tests correlate very well to the actual operation, but McClure indicates that simulation testing focusing only on specific processes has limited flexibility.
“A simulation study for a hydroforming operation cannot be applied with confidence to any other manufacturing process,” he says. “The lubricant requirements are completely different as compared to other metalforming applications.”
An example of a simulation test is the drawbead-simulator procedure, which determines the coefficient of friction for forming lubricants on sheetmetal. McClure says, “The drawbead test involves pulling a metal strip through a die,” McClure says. “It mostly evaluates the lubricant under mixed film and hydrodynamic conditions, and does not generate sufficient temperature and pressure to activate most extreme-pressure additives.” Lubricants are compared based on their coefficients of friction determined by the test.
Lab-bench tests are not used to study process variables but rather focus on fundamental phenomena over the entire spectrum of lubrication regimes. “If the user understands where the results from a specific bench test can be applied, there is potential to achieve good correlation with field trials,” McClure says. “The large number of available lab-bench tests provides a good deal of flexibility to generate data that might be pertinent to a specific metalforming operation.”
A lab-bench procedure that provides useful information in evaluating metalforming fluids is the twist compression test. This technique measures the transmitted torque between a rotating annual cylinder (tool) and a lubricated flat-sheet specimen. The lubricant, tool and sheet materials can be varied.
Pressure can be adjusted to 50,000 psi to best duplicate the actual conditions of the metalforming process. The coefficient of friction also is calculated in this procedure by determining the ratio of the transmitted torque to applied pressure. Fig. 3 shows a twist compression tester.
“Data can be taken as the test specimen passes through four stages: initial contact, primary lubricant mechanism, lubricant depletion and lubricant breakdown,” McClure says. “The value of the process is that it can evaluate lubricant performance down to lubricant starvation and boundary conditions. At that stage, metal-to-metal contact is obtained as the lubricant is squeezed out from the contact zone.” Lubricants can be compared based on how long they can resist breakdown under severe conditions.
The twist compression test should be conducted in a comparative fashion using a reference lubricant. McClure believes that this lab-bench test offers more flexibility and can correlate with actual field operations, if used properly.
Continuing improvements in manufacturing efficiency and in the types of metal alloys used will challenge metalforming lubricant suppliers to develop products that meet the diverse needs of these applications. Systematic evaluation of these processes, combined with thorough testing, will enable the industry to respond with the proper recommendations in the years to come. MF
Neil Canter heads a consulting company, Chemical Solutions, Willow Grove, PA. He can be reached at neilcanter@comcast.net.
Industry-Related Terms: Alloys,
Bending,
Blanking,
Case,
Coining,
Die,
Draw,
Drawing,
Forming,
Hardware,
Notching,
Run,
Spectrum,
Springback,
Strips,
Surface,
Torque,
Twist,
ViscosityView Glossary of Metalforming Terms
See also: ETNA Products, Inc., Henkel Technologies
Technologies: Lubrication