Tandem-to-Transfer Transition Kicks Class-A Stamping Line Up a Notch
December 1, 2008 Stamping large closures and one-piece body sides for local OEMs has Magna's Mexican operations investing in automation to wring as much productivity from its press lines as possible.
Magna operates automotive stamping and assembly plants all over the world. And, manufacturers of metalforming and automation equipment are hard at work developing the products needed to support the company’s global expansion efforts. This often requires the coming together of vastly different cultures, whether Eastern or Western European, American, Canadian, Mexican or Asian. The successful integration of new, complex automation products into a pressroom requires close cooperation of all parties involved—the equipment provider, installer and the customer, regardless of their nationalities and individual business cultures.
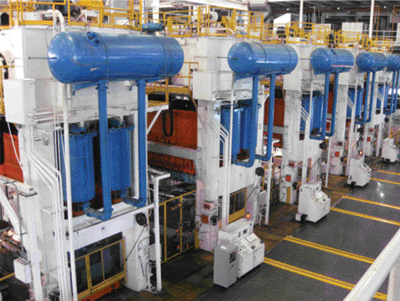 |
This five-press line at Estampados
Magna de Mexico produces Class A automotive panels. Originally set up
as a tandem line, it now runs more like a transfer line—more quickly
and smoothly than ever before—thanks to new automation added to the
line earlier this year. |
One recent case illustrates this point well: integration of new transfer automation by Swiss manufacturer Gudel at one of the newer Magna automotive-stamping and assembly plants in Mexico. The installation and five-month ramp-up earlier this year of Gudel’s roboFeeder transfer units have dramatically improved process flow along a five-press tandem line at the Estampados Magna de Mexico plant in Ramos Arizpe, Coahuila, Mexico. Swiss, American and Mexican engineers worked hand in hand with Magna personnel from Mexico, Canada and the United States to ensure that the line upgrade yielded the expected productivity gains.
“We’ve doubled output from the line,” says plant general manager Roman De La Torre, “in part because our line operator can troubleshoot the entire line in less than 3 min. working from one control console.” Originally, according to De La Torre, the operator had to walk the entire five-press line and survey four different control consoles to troubleshoot. This could cause the line to be down for as long as 15 min. “The significant improvement in the trouble-shooting process came about thanks to the close cooperation of all parties involved in upgrading the tandem line,” he says.
Huge Stampings: One-Piece Body Sides for GM
The Estampados Magna de Mexico plant in Ramos Arizpe, acquired by Magna in 2004, provides Class A stampings and assemblies primarily to the nearby General Motors assembly facility (for the Vue and HHR vehicles), as well as to neighboring Chrysler and Nissan plants. Its 360,000-sq.-ft. plant houses 38 presses from 150 to 1500 tons, including a pair of huge tandem lines, each with five 1500-ton mechanical presses. A 180-in. tandem line stamps primarily one-piece body sides, as well as hoods, doors and floor pans. It is this massive line that Magna chose to upgrade with new transfer units.
“Originally outfitted with two-axis loader/unloader units to move the stampings from press to press along the tandem line,” says De La Torre, “the line produced at a rate of 3 to 3.5 strokes/min. But producing just-in-time for General Motors, by far our largest
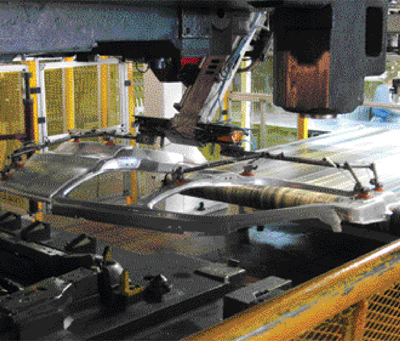 |
Among the products formed along the
newly automated tandem line are one-piece body sides, shown here, as
well as hoods, doors and floor pans. |
customer, required that we ramp that line up to at least 5 strokes/min. Replacing the two-axis transfer units with the Gudel roboFeeder units, plus the technical support received from Gudel’s Mexican office, allowed us to surpass that goal, to 8 strokes/min., with the capability to get to 10 strokes/min. once we fine-tune the destacker and the dies. This gain in throughput has opened up a lot of production capacity on that line, which we now market to our customers looking to source more large stampings.”
The roboFeeder transfer system is designed to make tandem lines function as transfer lines, since its motion is synchronized with that of the press rams. Parts transport directly from one die station to the next without the need for intermediate stations between presses. All servo motions of transfer link via a virtual encoder, say Gudel officials, which then is synchronized electronically to the angle of the press. “This is where the increase in line speed comes from,” says De La Torre, “as the transfer arms can reach into the presses as the rams continue to cycle.”