In other words, turnkey systems come in a range of variations. “Automation used to be something that you applied only to dedicated high-volume applications,” explains Josh Dixon, director of sales and marketing at Beckwood Corp. (www.beckwoodpress.com). “With decreasing prices for collaborative robots, conveyors and vision systems, automation is more flexible than ever and can be adapted to fit lower-volume, high-mix applications.
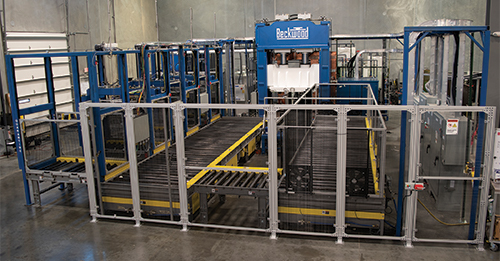
|
The fully automated titanium forming cell includes a custom hydraulic press, heat control, conveyor system and automated die change.
|
“If the goal is to provide a safer work environment,” Dixon continues, “and the goal is to eliminate the handling of heavy tooling, there’s automated die clamping and unclamping, storage and retrieval. Or, to eliminate downtime, today’s sensor-equipped presses provide predictive-maintenance capabilities, monitoring press components and anticipating part failure based on wear patterns well before the system goes down. Bottom line: Every customer comes to us with a goal in mind for achieving a competitive advantage. Our job is to design a solution to achieve their end goal.”
“Customers look to us to help with press transfer systems, pick and place automation, index tables and a lot of quality assurance,” says Jon Schmidt, PE, chief engineer at Neff Press, Inc. “With the right sensors, you can use a force-over-distance curve and compare that with the estimated baseline to know if you made a good part, even before placing it in an inspection station.
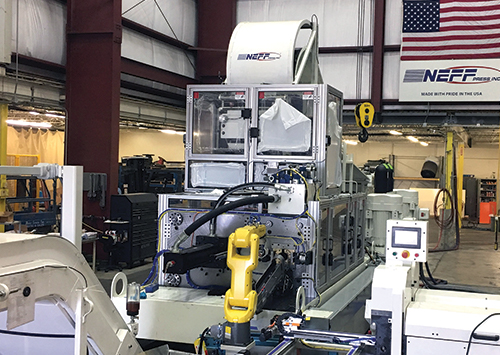
|
This horizontal hydraulic turnkey press includes the coil feed, tooling, robot, conveyance and a trim-and-dimple station.
|
Talking Turnkey
What do metal formers need to consider when investigating turnkey hydraulic press systems? Here is what the press experts have to say.
“Have a defined goal and don’t lose sight of it. It is easy to get mesmerized by all of the possibilities when it comes to automation. So get your group together, have a brainstorming session and come away with clear goals to drive your buying decisions.”
—Josh Dixon, director of sales and marketing, Beckwood Corp.
“Before reaching out to the press suppliers, determine your budget, production rates and return on investment. Then we will work with you to design and build not only the right press or presses, but the right turnkey automation to support them as well.”
—Rob Bisbee, automation team leader, Greenerd Press and Machine Co.
“Consider your volume. If you are producing 400,000 parts annually, then full automation may not be for you. In addition, consider your workforce. We can put together systems that process raw coils from start to finish, but they require a higher level of skill and knowledge versus semiautomated systems with intermediate sites where associates perform various tasks.”
—Jon Schmidt, PE, chief engineer, Neff Press, Inc.
“Think about available head and floor space for the equipment, as well as internal logistics. For example: If it’s a coil-fed line, how will those coils be brought to the line and how will finished product be moved from the line without interrupting production?”
—Ray Fausz, vice president of sales, Sutherland Presses
|
“Force-over-distance sensing,” Schmidt continues, “utilizes press-mounted stroke and tonnage feedback devices, coupled with data acquisition, to compare a press-fit or forming curve to established norms. Applications like bearing insertion, crimping, staking and deep-draw forming are good candidates for this technology which, in some cases, has completely eliminated destructive testing of samples, making inspection gauges obsolete.”
Meeting Challenges
Not only do customers expect their press suppliers to be equipment experts, but process and materials experts as well, notes Greenerd’s Josefiak. “For example: A customer, experiencing problems with part handling due to a vacuum-cup-equipped gripper system that couldn’t consistently secure the parts because of the thickness of the lubricant, sought a solution. We were able to design custom end-of-arm tooling that provided a mechanical grip on the edge of the material, resulting in effective gripping of the parts.”
Another challenge, this one met by Beckwood, came in the form of worker safety concerns. Wabash National, a producer of semi-trailers, machines large tank heads ranging in size from 24 to 160 in. using a 3500-ton hydraulic press. With the prior setup, an operator had to climb into the machine to fasten a tool or load a part.
“We added a bed trolley that shuttles the lower tool in the bed for tool change and part loading and unloading,” says Dixon. “Now, the company loads with an overhead crane and suction cups, placing tools onto the bed and shuttling the press bed back into the press to form the part.”
No discussion on automation is complete unless it includes Industry 4.0 and shop-floor connectivity. “Control systems have become extremely important,” says Sutherland’s Fausz, citing flexibility and connectivity as critical features. Sutherland’s software-based I-Press for press-speed control, tank monitoring and more, allows for changes on the fly. “Think of it like an iPhone,” he says. “When you want to add capabilities to your phone, you don’t call the app store and ask for a chip. Instead, you simply download the app. The same is true of the I-Press.”
Fausz adds, “Full press controls interface with all outside automation. Consequently, I-Press manages the entire line, allowing the operator to monitor everything from the press’s main operators station, and the software allows for additional capabilities, available on Rockwell Allen Bradley, Omron and Siemens platforms.”
“New for 2020, cool stuff for hydraulics—flow temperature, leak detection, etc.—the result of working with Balluff,” noted Mark Sutherland, the company’s CEO, during FABTECH 2019 in Chicago: “Our I-Press package,” adds Jack Wilson, the company’s president, “provides a simple path for smart predictive presses, which will communicate between facilities, enabling remote troubleshooting before there’s trouble.”
Last, but certainly not least, automated turnkey systems enable some companies to reverse outsourcing. “Vertical integration allows companies to consistently process parts in house,” says Neff’s Schmidt. “The technology costs a lot, but so does outsourcing. We’re seeing companies reshoring and bringing production back from Asia thanks to automation.” MF
Industry-Related Terms: Bed,
CAD,
Die,
Drawing,
Edge,
Form,
Forming,
Staking,
Stroke,
Thickness,
Transfer,
Hydraulic Press,
Lines,
RunView Glossary of Metalforming Terms
See also: Greenerd Press & Machine Co., Sutherland Presses Inc., Neff Press, Inc., Beckwood Press Company
Technologies: Coil and Sheet Handling, Pressroom Automation, Sensing/Electronics/IOT